Detailed Product Description
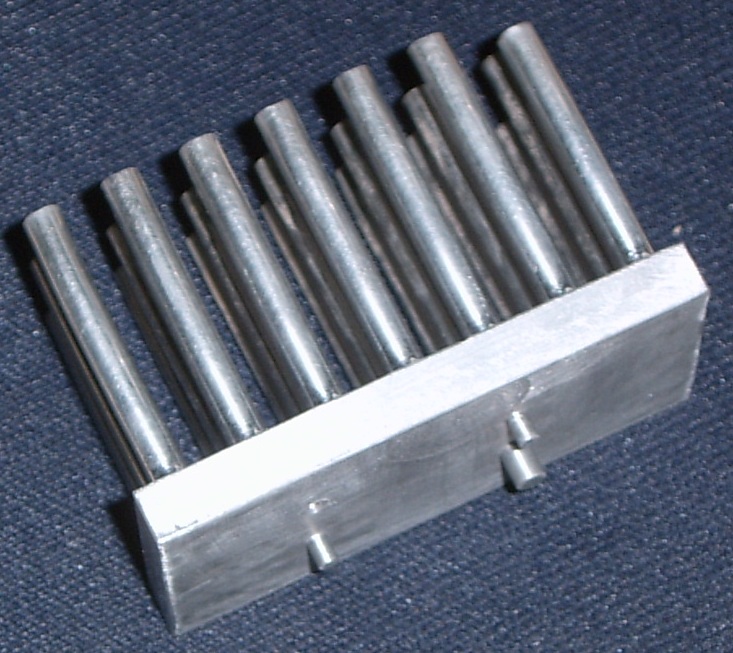
Pin fin design:
- Pin fin heat sinks are considered to be among the most powerful heat sink designs available today
- Pin fin heat sinks provide very low thermal resistance values per given space and low pressure drop
- The cooling capabilities of pin fins stem from the round geometry of the pins, the omnidirectional pin configuration, and the use of highly conductive materials
- The smooth round pins reduce resistance to incoming air streams and enhance air turbulence between the pins
- The omnidirectional structure maximizes the entrance of fresh air into the pin array and at the same time allows the hot air to exhaust from the pin array in every possible direction
- The use of highly conductive materials further reduces the thermal resistance of the heat sinks
- Googe has further enhanced the performance of pin fin heat sinks via the introduction of the splayed and flared pin fin designs
- Their unique structure allows them to offer lower thermal resistance values and lower pressure drop per given space
-
Forging:
- The Cold Forging process is used in the manufacturing of the majority of Googe heat sinks
- The process ensures that no air bubbles, cavities or any other impurities are trapped within the material
- The cold forging process allows for the use of highly conductive copper and aluminum alloys
- Aluminum pin fin heat sinks are forged from pure aluminum (AL1100)
- The thermal conductivity of AL 1100 is 1510 btu/in ft2 hr of. (~50% higher than AL 380, a common cast alloy)
- Copper pin fin heat sinks are forged from pure copper (CDA 110)
- The thermal conductivity of CDA 110 is 2712 btu/in ft2 hr of. (~100% higher than AL 380, a common cast alloy)
Benefit:
Complete in one piece with no interface.
High aspect ratio 1: 100
Can forge aluminum alloy, pure aluminum and copper
No taper fin shape improves airflow smooth through
High material density increases thermal conductivity
Wide range geometry as die casting
Fin or pin forge only one time doesn't need cross cutting
-
Type
|
Pros
|
Cons
|
Forging
|
No interface
High density
High aspect ratio 1:100
Wide range geometry
|
Tooling developing required 3 weeks
|
Extrusion
|
Cost effective
No interface
|
Lower aspect ratio 1:23
Tapered fin decrease air flow in-take
|
Die Casting
|
Cost effective
Net shape
Less machining cost
|
Poor density
Poor heat transfer performance
Lower aspect ratio 1:15
|
Stamping/ Soldering
|
Cost effective
High fin
|
Too many interface
Un-reliable quality
|
Skiving
|
High fin
|
Potential crack risk between fin and base
Secondary operation required
|
Maching
|
Fliexible applications
|
Cost expensive
Long lead time
|
|